We provide custom solutions to all our customers and offer complete technical advices that your company can take advantage of.
In the realm of extrusion molding, twin screw extruder barrels stand as indispensable components, collaborating with screws to transform polymers into their final form. By understanding the intricacies of these barrels, we can gain valuable insights into the extrusion process and optimize its efficiency.
Structure of Twin Screw Extruder Barrels:
Twin screw extruder barrels typically exhibit a straightforward design, composed of several sections in larger machines. This modular approach facilitates machining but presents challenges in ensuring consistent dimensions and concentricity across the sections. Furthermore, flange connections introduce complexities in arranging heating and cooling systems, potentially compromising temperature uniformity. To address these concerns, some large extruders employ inner liners or cast wear-resistant alloy layers, while the outer casing may be constructed from ordinary steel for cost-effectiveness.Feeding Mechanisms:
The feeding mechanism plays a pivotal role in ensuring a smooth and continuous supply of material to the extruder barrel. Among the prevalent options, common-style feed hoppers offer simplicity and affordability, particularly for smaller extruders. These hoppers rely on gravity to deliver material into the barrel. However, the risk of material bridging within the hopper can disrupt the extrusion process.Forced-feeding hoppers, often employed in large extruders or when handling powdery feedstock, address this limitation. A motorized screw, driven by a gear reducer, propels material into the barrel. When the barrel is full, the opposing pressure from the material halts the screw rotation. As the material level depletes, the spring-loaded screw resumes operation, maintaining a consistent feed.
Vibration-assisted hoppers, characterized by their simplicity, incorporate an electromagnetic vibrator into the standard hopper design. When activated, the vibrator induces horizontal oscillations, enabling material to overcome frictional forces and enter the barrel. This method proves effective for both powders and granules, minimizes bridging, and boasts a low-cost implementation.
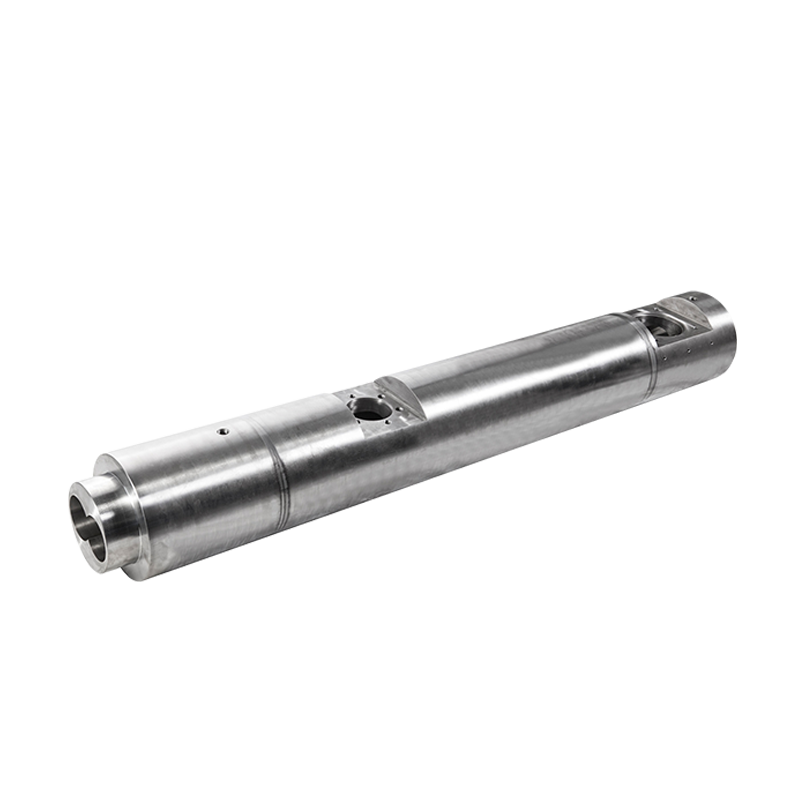
Common Issues:
Despite their robust design, twin screw extruder barrels can encounter various challenges that hinder optimal performance. Wear and tear, particularly in the intermeshing zone, is a prevalent concern, leading to reduced efficiency and potential material contamination. To mitigate this issue, abrasion-resistant materials and surface treatments are employed.Material bridging, particularly in common-style hoppers, can disrupt the feeding process, causing inconsistencies in product quality. Implementing forced-feeding or vibration-assisted hoppers can effectively address this challenge.
Non-uniform temperature distribution within the barrel can compromise the plasticization process, leading to product defects. Implementing effective heating and cooling systems, coupled with precise temperature control, is crucial to ensure consistent temperature profiles.
Twin screw extruder barrels serve as the backbone of the extrusion molding process, working in tandem with screws to transform polymers into their final form. Understanding the intricacies of these barrels, including their structure, feeding mechanisms, and common issues, is essential for optimizing extrusion efficiency and producing high-quality products.